coating integrity test|industrial coating problems : distributing Abrasion of a coating occurs when all or a portion of the coating is scraped off by another material, which is clearly undesirable because . See more WEB11 de dez. de 2019 · Disponível para slot machines Starburst (Netent), Joker's Jewels (Pragmatic Play), Spin or Reels HS (iSoftBet), Tundra Wolf (Playtech) e Eternal Lady .
{plog:ftitle_list}
webCriado em dezembro de 2018, na Linha Verde da Bahia, o circo possui, malabarista, trapezista, quatro palhaços, contorcionista, carro maluco, o cantor Zé Furico – que a .
Hardness is a mechanical property that helps a coating resist indentation. (A wider discussion of hardness can be found in the article 5 Ways to Measure the Hardness of a Material.) A harder coating has a greater ability to withstand depressions. When indentation is a concern it is worthwhile to use a coating . See moreAbrasion of a coating occurs when all or a portion of the coating is scraped off by another material, which is clearly undesirable because . See moreThe ability of a coating to adhere to a base material is extremely important because without an adequate adhesive bond, the coating could . See moreWhen coatings are applied to base materials that will undergo deformationthen it is imperative that the coating be able to . See more
This is accomplished by providing job documentation, including a commentary on the type and adequacy of equipment at the jobsite, the rate of work progression, information regarding .
In this video described about #Coating_Integrity_Test #CIT,#CIT_Test , #3LPE_Coating #HDD, #Horizontal Directional Drilling , #Shallow_. #Piping_Tech_Master [email protected]. 89 TESTING LABORATORIES IN 57 FACILITIES IN 21 COUNTRIES WORLDWIDE Coatings/Polymer Laboratory (13) Metal Laboratory (35) . integrity. With more than 95,000 employees, SGS operates a network of .
The Food and Drug Administration (FDA) acknowledges this iatrogenic complication and continues to work with stakeholders on standards related to polymer coating integrity.3 In 2010, the Association for the Advancement of Medical Instrumentation (AAMI) established particulate generation testing as a standard for evaluating coating integrity of intravascular .Enamel rating is a standard industry test that checks the integrity of protective lacquer/enamel on metal packaging. . The value of the resulting current flow indicates the degree of metal exposure or porosity in the coating. Smithers is able to test flexible aluminium tubes in accordance with BS EN 15384-1 using a sodium chloride electrolyte .
integrity concrete coatings reviews
Additionally, the article outlines the importance of experimenting and testing methods applied by Shawcor and CSNRI to prove the performance of composite technology being used for pipeline integrity repairs for 20+ years. Such technology provides mechanical protection of pipeline coatings installed via trenchless methods.Pipeline integrity will be improved by providing coatings that will not be damaged during installation and eliminating conservatism in . Summary of Test Results Results of tests on coating systems are summarized in this section. Complete test data can be obtained from the PRCI. J. D. Hair & Associates conducted rotary abrasion testing at a .Sheath Resistance testing is often used by Network Rail to test the sheath integrity of their . provides a semi-conductive layer through which to pass the potential current across and in order to undertake the test this coating has to be rubbed off across a pre-determined length. The voltage applied is determined by the minimum average .
Coatings isolate the metal from electrolytes in the soil, thus reducing the power requirements for CP; the CP protects the metal exposed to the environment at coating holidays (defects/holes, etc.). New pipe coatings may provide 99% of the pipe protection, but as they slowly deteriorate, the CP system provides more and more of the protection.
To explore the effect of coating methods on membrane integrity, we compared the ratio of full cell membrane coating of three methods: sonication, extrusion and a combination of these two .

Certain painted, coated or lined plant and equipment is subject to aggressive working duties or harsh environments, such as a chemical process or a buried pipeline and require a continuous paint, coating or lining film to protect the underlying substrate, maintaining its integrity.. Holidays. A paint, coating or lining must be applied as a continuous film to .Corrosion Control -Integrity Management. Operating Conditions. Maintenance Plans. Inspection Plans •Radiography . COATINGS CATHODIC PROTECTION INTEGRITY . ASSESSMENT OF BURIED PIPELINE THRU PIPE COATING SURVEYS / CIPL . Test pressure – Residual thickness. N/mm2 mm. 10.0 ≥0.6. 10.0 ≥0.6. 0.1. ≥0.6. 10.0. This study is an investigation of (1) the mechanical behavior of Cr-coated cladding under RCT and its FEA modeling; (2) characterizing failure behavior of the coating layer and resulting failure of the underlying Zircaloy cladding; (3) unveiling the mechanism of the underlying Zircaloy cladding failure induced by the surface coating; and (4) the effect of coating .Adhesion testing is also a valuable indicator for determining the integrity of coating systems that have been in service for extended periods of time, may require maintenance, and overcoating is a strategy being considered; and is frequently used during coating failure investigations. . Precautions are included regarding the use of the test .
The intention of this document is to review the current regulations surrounding coating integrity as it applies to trenchless installation methods, the proposed changes to that regulation, and to evaluate the effectiveness of the PRCI study. It will be clear that the current regulations do not address coating damage during trenchless construction.The test standard describes in-vitro test procedures for assessing the acute coating durability of coated drug-eluting vascular stent systems. Clinical performance (i.e., drug elution) may be affected by coating durability. .Stent Coating Integrity of Durable and Biodegradable Coated Drug Eluting Stents J Interv Cardiol. 2016 Oct;29(5):483-490. doi: 10.1111/joic.12303. Epub 2016 Jun 10. Authors Saami K Yazdani 1 . Materials Testing / methods Models, Anatomic Rabbits . The first introduction of the scratch test as a qualitative method of measuring coating adhesion was in the 1950s by Heavens [1] who applied a constant load to the sample surface via an indenter in order to damage the surface by scratching and induce delamination of the film.The applied loads that created specific damage, especially cracks or delamination, .
The coating's integrity is evaluated utilizing non-destructive testing (NDT) methods that don't disturb the underlying substrate. The goal of NDT is to find flaws or irregularities that can't be seen by the human eye using various technologies. FDA said coating integrity testing should be conducted if a device has any coating along the length of the catheter or on the balloon. Noting that coatings are intended to improve device performance, FDA said degradation could negatively impact patient safety, causing embolization risk for example. Assessment of baseline coating integrity .Integrity Coatings is a leading manufacturer and supplier of countertop and bathtub refinishing coatings for kitchens and bathrooms. Place your order now! (214) 631-8717 A. The best spot test for the presence of hexavalent chromium uses 1,5 diphenyl carbohydrazide. A suitable test (even though it is directed at coatings on zinc, cadmium and aluminum) is described in ISO 3613, Test Solution C ff.This test will work fine on silver.
Testing methods employed to ensure the integrity and consistency of metal coatings on plungers in electronic devices can vary depending on the type of coating being used. For example, a coating composed of a combination of metals and polymers may require a different set of tests than a single metal coating.
Testing Hydrophilic Coatings Testing Hydrophilic Coatings Performance testing hydrophilic coatings will ultimately be based on your requirements but will always involve testing for lubricity (slipperiness) and durability. When wet you can feel the difference the lubricious hydrophilic coating makes. The ISurGlide hydrophilic coating swells with
Clinical performance (i.e., drug elution) may be affected by coating durability. Balloon-expandable and self-expanding stents are included within the scope. Recommended practices for assessing acute coating durability include baseline (deployment) testing and simulated use testing. We provide several approaches for coating integrity assessment.the peeling of coatings reported in MDRs included the persistence of coating fragments in patients, some of which required surgical intervention to mitigate the consequences, adverse tissue . External coating testing for pipeline directional drilling installations or informally "Bore Test". It is a very much requested test in Alberta, Canada. The conditions of the installation are severe for the integrity of the external coating. So, a procedure has been developed after the involvement in several projects.
Pressure sensitive tape is applied and removed over cuts made in the coating. There are two variants of this test; the X-cut tape test and the cross hatch tape test. The X-cut tape test is primarily intended for use at job sites. Using a sharp razor blade, scalpel, knife or other cutting device, an X-cut is made through the coating down to the .
Portable Digital Refractometers distributor
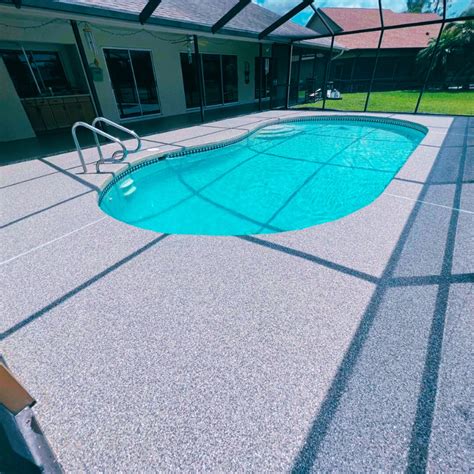
Auto Abbe refractometer distributor
webCom 75% do parque em funcionamento e previsão para entrega de 100% em março, o Kawana Park tem capacidade para receber até cinco mil pessoas por dia. Entre as .
coating integrity test|industrial coating problems